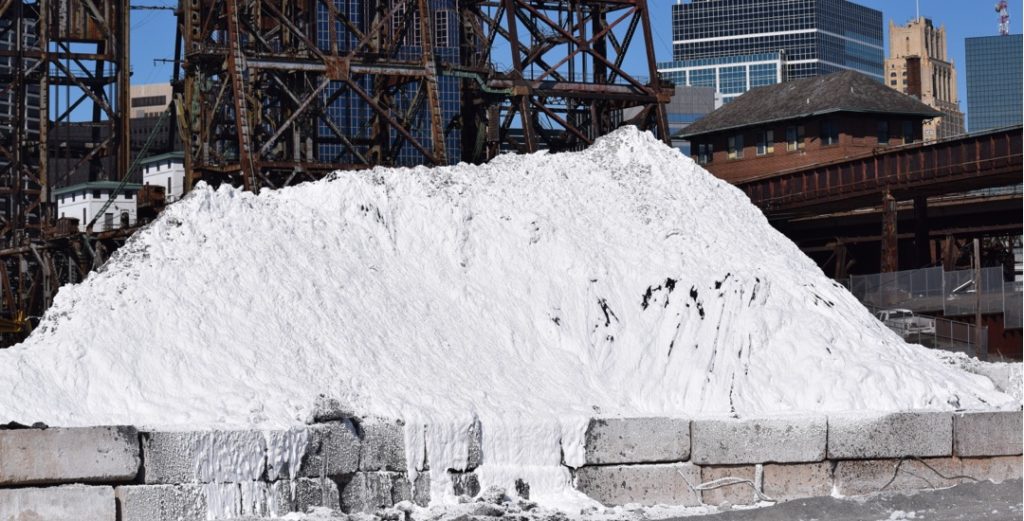
For 61 years, one of New Jersey’s public utilities operated a manufactured gas plant (MGP) on the right bank of the Passaic River, a stone’s throw from central Newark.
Squeezing gas out of coal had been the best way to heat homes and cook meals until natural gas emerged as the superior fuel in the mid-20th century.
MGPs closed in droves in the intervening decades, including this one in 1987. But it left behind a nasty yet familiar legacy of any MGP: coal tar in the topsoil.
Left unchecked, this byproduct of gas manufacturing can leach into groundwater or, when exposed, release foul smells and dangerous vapors. A badly needed remediation finally launched in 2020.
Action plan: open-air in-situ soil stabilization
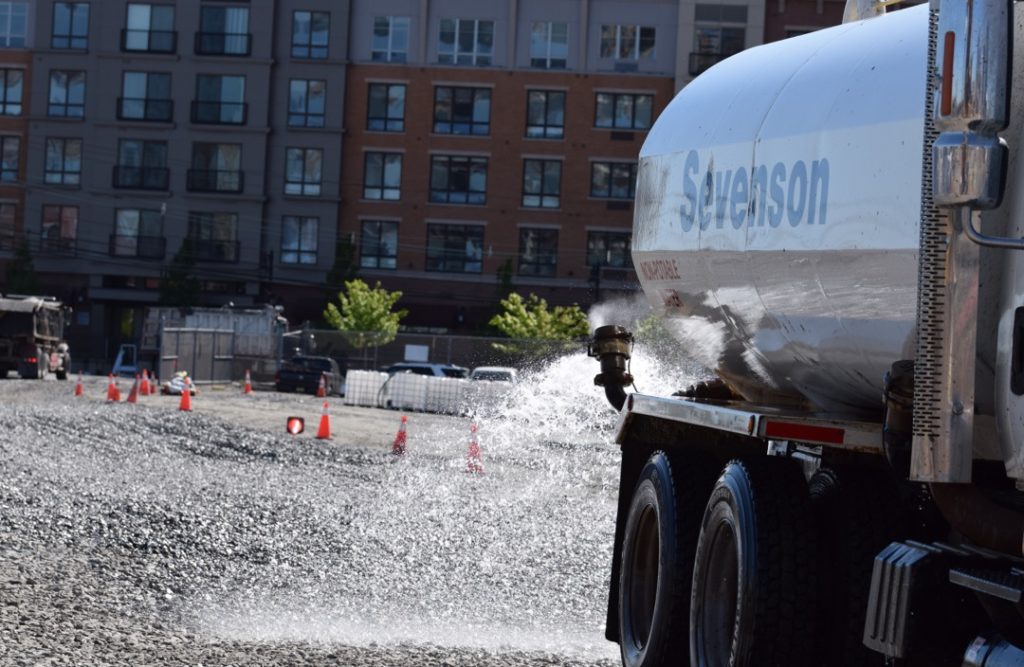
Excavating impacted soil and replacing it with clean fill is the traditional remediation method, but it wouldn’t work here because there was so much of it to move.
Instead, in-situ soil stabilization (ISS) was identified as the ideal remediation. In this process, the impacted earth is left in place and injected with specialty grout that prevents leaching once it cures.
Generally, ISS remediation is less than half as costly as excavating impacted soil and replacing it with clean fill. A more economical model, maybe, but also more complex. Only exceptionally skilled contractors can do it, and they require some exceptional products and equipment to do it right.
But Sevenson Environmental Services’ bona fides speak for themselves.
Founded in 1917, the company has been a major environmental remediation player practically since that category emerged in the 1970s. (Sevenson was among the specialists contracted for the cleanup of the infamous Love Canal dumping ground in Niagara Falls, NY — the country’s first Superfund site.)
They had two options:
- One option was to stabilize the soil under the cover of massive white tents. These tents — and the air filtration systems often accompanying them — are an effective method for containing dust, odors or harmful vapors.
- The other option was to remediate in open air, relying on portable measures to keep odors and VOC emissions under control.
Sevenson chose the latter due to the sheer volume of impacted soil they needed to address. At over 410,000 cubic yards, this is the largest active ISS project in the country. It would be faster, Sevenson reasoned, to do the work continuously instead of stopping and re-starting work every time a tent was dismantled and relocated.
And because they chose ISS over conventional excavation, the project would generate far less truck traffic, reduce fuel use and labor hours, and eliminate the need for added odor and vapor control for impacted soil in transit.
It all hinged on whether Sevenson could keep odors and vapors in check.
Foam coverage is essential to stopping odors and vapors
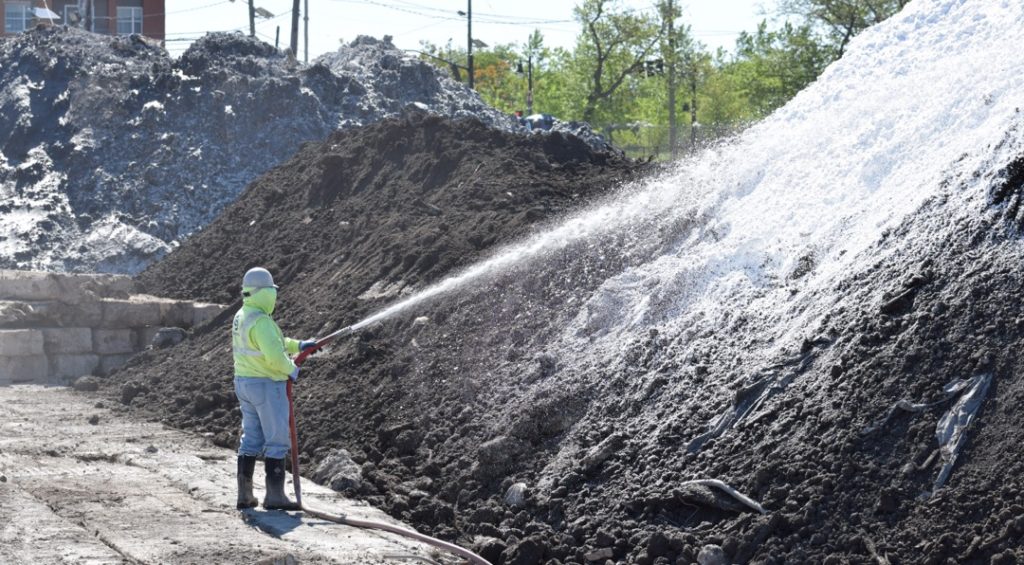
Though the bulk of the impacted soil at this former MGP site will stay where it is, excavation of topsoil to prepare for ISS is still necessary.
Atmos Technologies’ trailer-towed PFU 400/25 foam application system was among Sevenson’s initial fleet of equipment brought to the job site.
To keep odors and vapors from escaping the work site, operators use the system to spray Atmos Shield 645 Foam Concentrate over excavated piles as well as over the earth exposed by the digging. The water-based foam solution provides immediate suppression of odors, dust and VOCs.
Sevenson was familiar with this equipment and product, having utilized it on a handful of prior remediation projects.
An alternative mist odor control product rounds out remediation
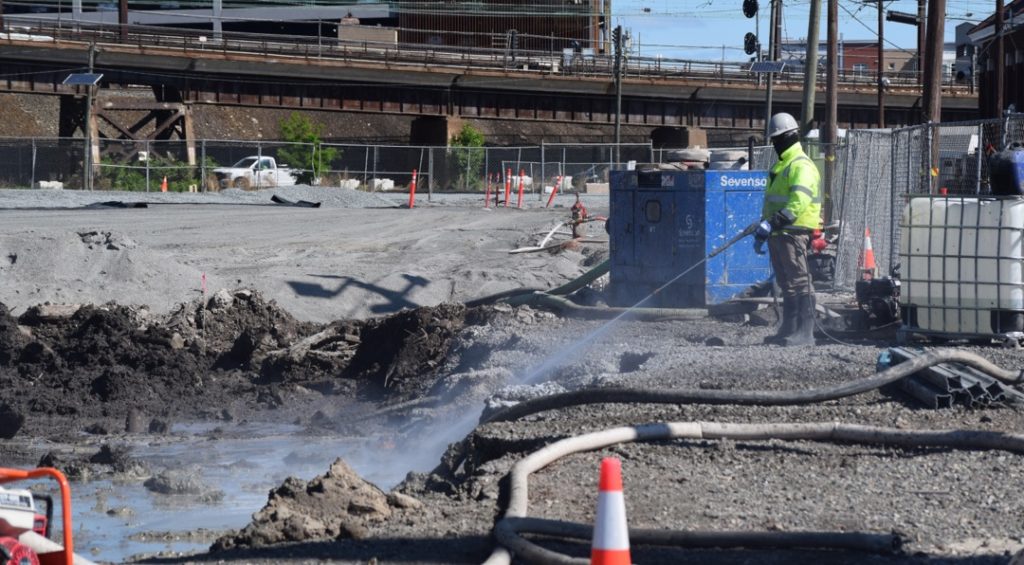
Spraying foam over impacted soil was not the only necessary measure taken at the site. The process of digging into the ground and hauling out dirt results in the release of strong odors and vapors that must be treated right away.
To do this, crews utilized odor-neutralizing mist that’s sprayed directly over the working area during excavation. Sevenson had already lined up a provider of this chemical and system prior to work beginning.
But shortly after excavation began, Atmos representatives asked whether Sevenson was interested in trying one of our mist odor control products instead. We felt our SLSuper Neutralizer Concentrate would work better, and we knew that Sevenson wouldn’t need to use as much volume of product if they switched.
Sevenson agreed to conduct a comparison of the chemicals to see which worked best. Importantly, a third-party consultant and the project’s community liaison each attended the experiment. Given the high volume of odor neutralizer this project would require over time, improved performance at lower doses could represent a significant savings that Sevenson could pass along to the utility.
The experiment confirmed our suspicion. Agreement among Sevenson, the consultant and the liaison was unanimous: Gallon for gallon, the oil-based SLSuper we suggested performed better.
Sevenson estimated that making this switch resulted in a 15% savings on the $3 million they expected to spend on such chemicals. $450,000 is nothing to sneeze at, but additional savings on the horizon might make it look like pocket change.
Reaping the rewards of speed
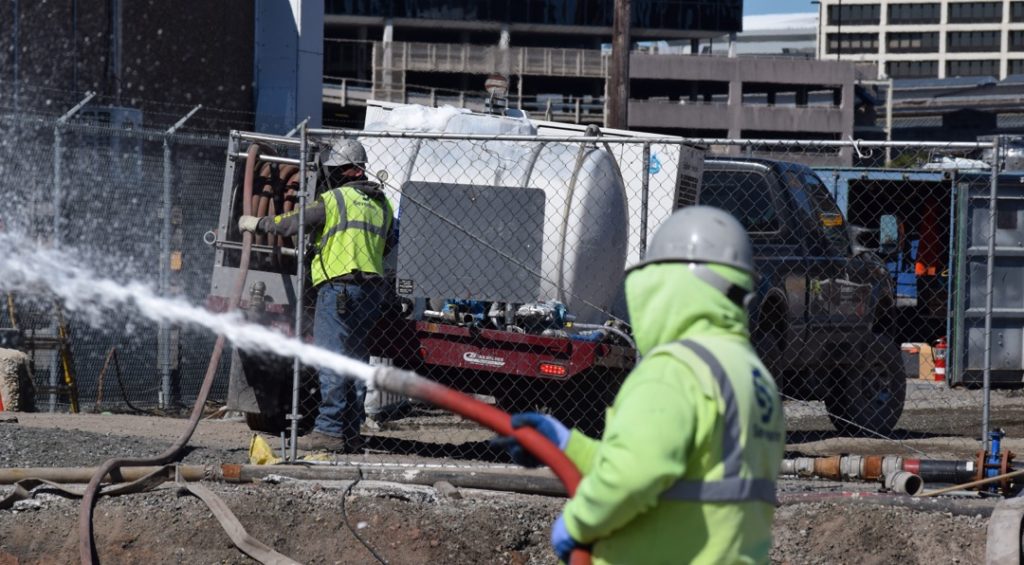
Now sourcing both the mist odor neutralizer and the foam coverage chemicals and equipment from a sole supplier, Sevenson reduced some of the administrative and logistical burdens on their project management team. The cost of all the equipment and all the chemicals is covered under one usage agreement.
But as the project progressed, it became clear that the decision to address odors and vapors with portable equipment in open air would pay off, too.
Due to the toxicity of the soil at the site, the project’s initial contract stipulated that no excavation area could exceed 10,000 square feet. If it was any larger, an unacceptable volume of dangerous vapors could escape the work site if control measures failed.
But Sevenson’s team and the utility each realized that Atmos’s control measures performed so well they could bump that number up. With the utility’s permission, Sevenson’s teams began excavating areas as large as 30,000 square feet at a time without any additional release of dangerous vapors.
And because Atmos delivered temperature-controlled bulk storage tanks to the work site, Sevenson’s operators kept up with the increased pace and volume of foam coverage without any problems.
Sevenson was moving fast, and it had a significant impact:
- The work site features underground natural gas delivery piping that serves surrounding communities. Crews can only excavate after first cutting and capping the piping network.
- That means excavation could only occur from May to October, opposite the “heating season.” Prior to the heating season, Sevenson needed to re-install the gas lines.
- Taking advantage of permission to excavate larger areas, Sevenson finished their excavation-heavy first phase of the project two months early.
- Sevenson estimates daily operating costs at $80,000. Two months translates to a savings of around $3.2 million.
A community reclaims its space
Even now, the Passaic drifts past a work in progress. But that work is a lot farther along than initially planned.
Originally targeted for completion in March 2023, Sevenson wrapped up its remediation phase in late 2021.
That’s saved the utility a lot of money. Even better, it means any plans for the cleaned-up site can kick into motion sooner — no doubt a boon to the region’s economic forecast.
But the most important impact of an early completion?
A year of burden and bother on the thousands living and working nearby was shaved off the project.
For our part, we’re thrilled that our products and equipment have helped make a difference on a project we know will help people take a part of their hometown back.
Interested in learning what new doors the right environmental remediation products and equipment can open for you? Let’s talk.