In recent years, the municipality of Montebello started a $5.4 million initiative to rid its neighborhoods of potholes.
Major streets were falling apart, spurring car accidents that averaged almost $600 per repair.
One winter, after bearing the weight of rush hour traffic, Montebello’s northern freeway caved into a 75-foot-long pothole.
The prevalence of patching and general road maintenance raised a red flag — and Mayor Kimberly Ann Cobos-Cawthorne got to work.
How HyRAP® benefits municipalities
The original plan was to uproot and reconstruct 34 major streets.
As Mayor Cobos-Cawthorne began vetting local pavement professionals, one bid stood out.
Its contents addressed every road her team sought to improve, plus an additional 44.
It detailed a process that entailed blending 100% recycled asphalt pavement (RAP) with rejuvenating oils to produce a pavement mix known as HyRAP® — which spreads over an Asphalt-Rubber Aggregate Membrane (ARAM).
The job would save Montebello $2.1 million. It came from Manhole Adjusting Inc., a construction group that works alongside Atmos Technologies to engineer multi-purpose, recycled asphalt pavement designs.
The benefits:
- Slash reliance on rock quarrying
- Reduce RAP Stockpiles
- Short-term street closures
- Streets with long life cycles
After briefing Mayor Cobos-Cawthorne on the eco-friendly nature of covering roads in HyRAP®, the duo won the contract.
And California’s first-ever 100% recycled asphalt street project was underway.
Recycled asphalt pavement dries in minutes
Street closures cause traffic jams, inconvenience drivers and restrict consumer activity.
While traditional hot mix asphalt settles within hours, larger projects like Montebello (35 centerline miles) might not harden for days.
City managers were sold on HyRAP®’s anti-skid and quick-cooling properties, as well as its ability to bear the weight of vehicles minutes after drying.
“The pavement process was very fast, with each step taking a day rather than weeks. Traffic was allowed back on [repaved] streets at the end of each workday,” said Mayor Cobos-Cawthorne.
Atmos helps pavement contractors develop and hone their own HyRAP® production process.
It starts by crushing, screening and sorting recycled asphalt based on rock density. Once the RAP is categorized, pavement contractors use Atmos’ production technology and apply Atmos’ rejuvenating oil to soften the aged binder — and restore its chemistry.
By engineering the proper mix design (aggregate size and binder ratio) and controlling the amount of oil added, you can produce various types of asphalt mixes to meet the performance demands of any road application.
The newly engineered mix design gave Montebello the ability to repave 78 streetscapes.
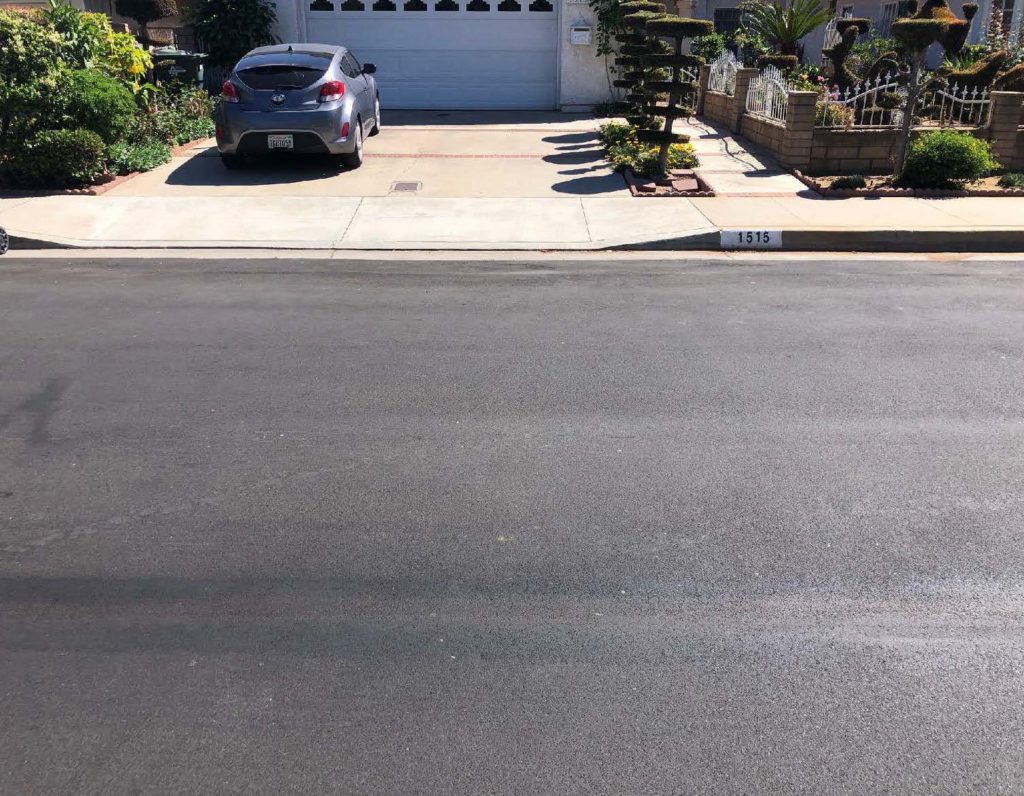
HyRAP® meets performance and durability standards
Although HyRAP® isn’t as common as traditional road improvement methods, data shows it performs well against natural wear and tear.
Like freshly mined aggregate, most recycled asphalt pavement (RAP) passes standard LA Abrasion and Micro-Deval Tests — confirming the materials’ toughness and abrasion qualities.
With total control of the blending process, Atmos can ensure every pavement blend is designed for longevity.
In Montebello, many cracked cul-de-sacs needed repair. To fix rounded streets, road menders needed a pavement mix that’s easy to spread by hand or trowel.
A mix with excessive rock content quickly stiffens and doesn’t easily shape. And an insufficient amount of rock creates a brittle, unreliable pavement.
By proportioning the rock and oil content just right — and having control of how much you need to produce — you cover more roads without sacrificing long-term durability.
A green way forward
Street infrastructure projects generate 100 million tons of asphalt rubble per year. From that amount, 80% gets recycled and trucked over to disposal sites.
If more municipalities pave roads with virgin aggregate, perfectly reusable asphalt will continue multiplying and releasing harmful fumes into the environment.
Atmos has the resources to completely restore the main aggregates and binders found in RAP, reducing reliance on new rock quarrying and mining.
It’s also common for RAP facilities to border job sites.
In California, Atmos partner Manhole Adjusting Inc. has a processing center to manage and screen the RAP.
This eliminated Montebello’s need to access virgin aggregate sources or quarries — and significantly decreased the cost and diesel emissions associated with trucking.
You could save millions on road improvement
The city of Montebello restored 78 streets and saved 40% with HyRAP®.
The My Montebello App, a digital forum that allows citizens to photograph potholes and submit work requests, decreased in activity since project completion.
Atmos Vice President of Procurement John Barry projects more recycled roads to be laid around LA county. Up next? Restoring a problematic highway shoulder lane.
If you believe recycled asphalt pavement may benefit you, we’d love to hear about your upcoming projects.