The debris left in the wake of Hurricanes Irma and Maria created a swell in the U.S. Virgin Islands’ (USVI) waste stream.
Remnants of buildings and uprooted trees cluttered the roadways, disrupting the lives of some 100,000 residents.
Many abandoned their vehicles and homes. The damages were irreversible.
In total, 72 miles of refuse needed to be disposed of — a logistical nightmare for a territory with finite resources.
“We’re running into the problem of space,” said Alice Krall, communications manager for the Virgin Islands Waste Management Authority (VIWMA). “The problem is trash being generated at amazing speed. We move it and it springs right back up.”
As dumps overflowed with mountains of debris, federal and local agencies scrambled to find neighboring countries with open capacity.
The longer the task force took to transfer refuse, the more hazardous stationary piles became.
It was the recipe for a severe environmental and public health crisis.
Changing the tide
Tropical storms weren’t the first to highlight the waste management system’s shortcomings.
Although the VIWMA’s working relationship with the EPA is improving, the underdeveloped Anguilla and Bovoni sites have been unsatisfactory for years. This is mainly because landfill surfaces are routinely left exposed, resulting in:
- Long spells of fire
- Littering scavengers
- Pervasive foul odors
- Other wind-borne materials
In recent years, however, the director of the VIWMA clamped down on the non-compliant dumps. The waste management team began sorting refuse, separating metals and instituting tipping fees. Compost and recycling programs are underway, too.
The director also saw a need for alternative daily cover. After consulting a group of engineers to adopt better practices and control environmental/public hazards, they recommended Atmos Cover ADC — a foam application that contains and protects residents from the dumps’ contents.
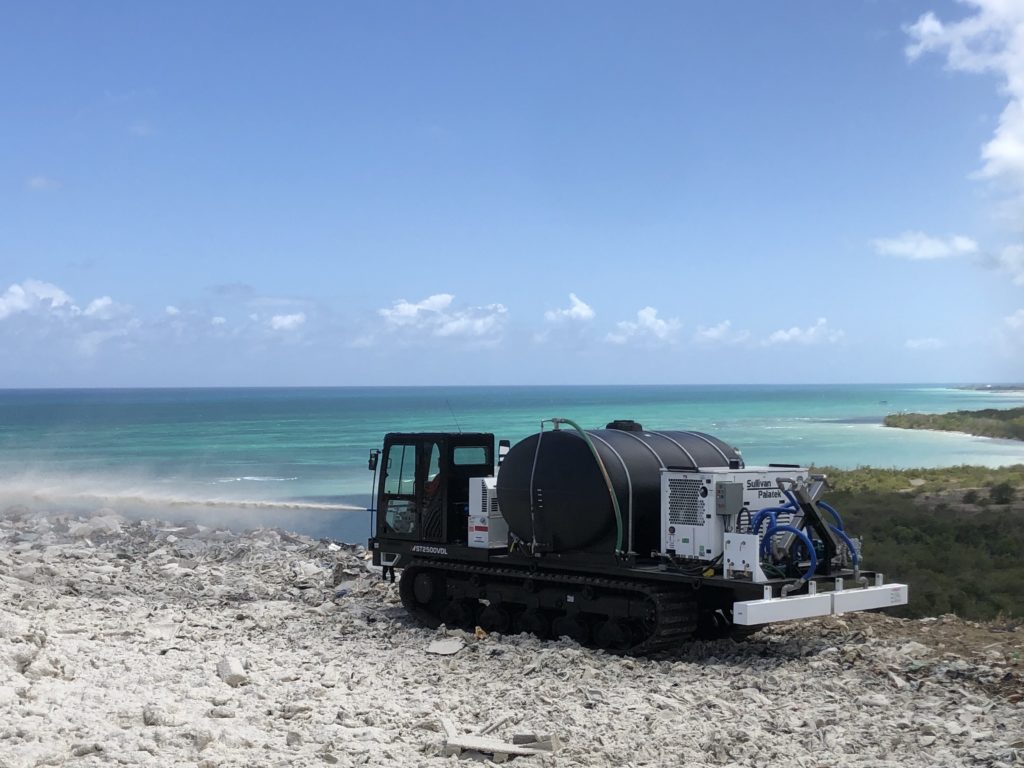
Slashing monthly soil expenditure by 83%
The logistics of importing good soil (compounded by scarcity) make it an expensive commodity.
Soil used in daily cover comes from pits outside of the islands. How well the soil controls fires, malodors and scavengers largely depends on its properties. These vary and aren’t always surefire.
The cost of securing high-quality soil falls anywhere between $150,000 and $200,000 a month.
Realizing this expense couldn’t be sustained, the director requested a consultation with Atmos to decrease reliance on traditional soil cover and loosen budget constraints.
Within a week, an Atmos technician was in the Virgin Islands to conduct a pre-site assessment. A custom-tailored solution that aligned with the VIWMA’s budget and goals followed.
Today, a Morooka-based Pneumatic Foam Unit (PFU) 2500 applies a layer of water-based foam at the Anguilla and Bovoni dumpsites.
The process takes one operator half an hour and, since 6 inches of daily soil cover is no longer needed, makes better use of the space. Of course, there were other challenges: The Caribbean environment poses year-round threats to landfill operations.
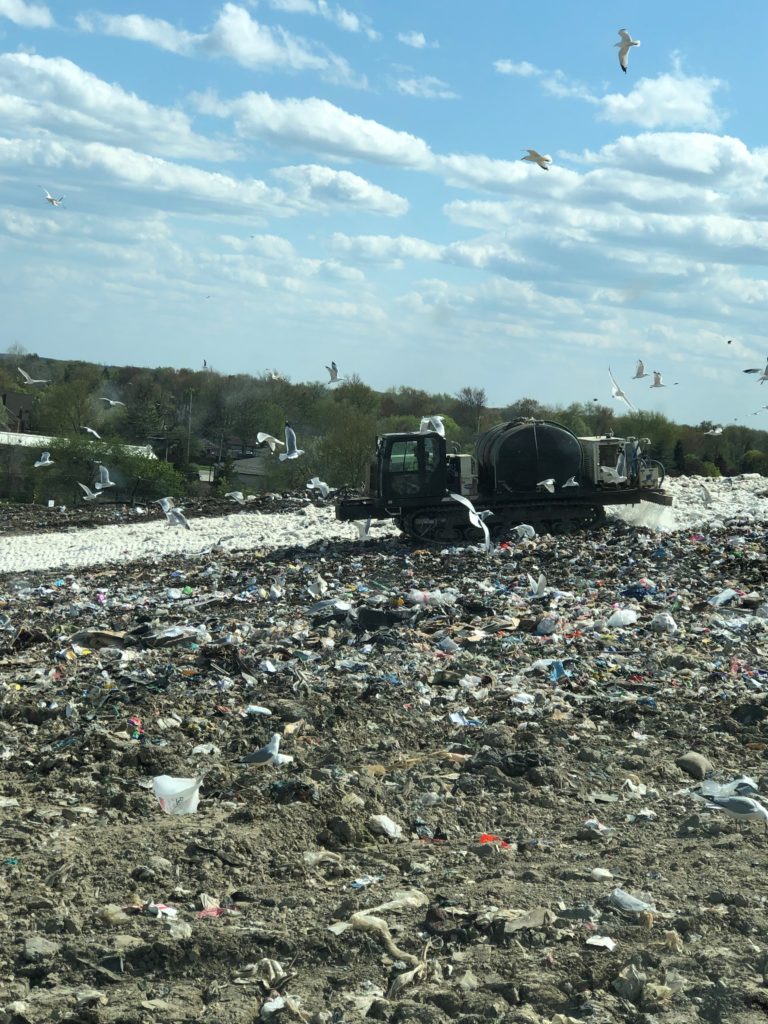
Taming landfill fires and unwelcome visitors
When pockets of methane meet rich oxygen concentrations under the Caribbean sun, underground fires occur. If untreated, parts of the landfill could cave in.
A subsurface cavity may be lethal. Landslides could shift heavy mounds of trash over the perimeter and crush passersby.
Personnel needs to know what lies underneath at all times to ensure safety.
The scrap metal sections contain another hazard. Fires originating from improperly disposed of cars — still containing batteries and flammable fuels — can take weeks to extinguish.
The director made controlling these spells of fire a priority and wrote Atmos’ foam solution into their fire plan. While the solution doesn’t contain every chemical found in common extinguishers — it certainly can suppress smoke emanating from hot spots.
It’s the first step in smothering fires, ultimately stopping toxic gasses from entering the public sphere.
The bird problem at St. Croix’s main airport
Hundreds of seabirds routinely swept into the dumps and scattered their meals abroad — dropping refuse into residential and municipal areas below.
Homes and businesses were covered in trash. The dumps already had a weak reputation among residents and not being able to control the scavengers only made things worse.
The larger problem? Aircraft safety.
The Anguilla landfill is situated beside a major airport runway. Too many birds in the air cause flight delays and, in severe cases, shutdowns.
The VIWMA expressed these concerns. Atmos’ field-proven alternative daily cover delivered.
The foam mixture naturally repels water, creating a 24-hour seal over landfill surfaces. It neutralizes and locks-in odors, redirecting all kinds of animals in the process.
But designing the VIWMA’s application required a unique detail. The on-site, chemical storage tank had to resist the force of a hurricane.
Securing alternative daily cover in tricky environments
One of the benefits of working with Atmos is receiving all application equipment at no charge (customers only purchase foam supplies as needed).
Some equipment, however, needs to be built from scratch to meet site requirements.
For the VIWMA, that meant repurposing a cargo container into a hurricane-proof Bulk Storage & Dilution System (BSD-7000) and bolting it down to concrete to withstand strong winds.
The custom-built storage unit would also serve as a stockroom with parts and tools to service the vehicle applicator.
Next, Atmos technicians trained the VIWMA on how to use all application equipment.
Other environmental solutions companies might see a disadvantage in partnering with an isolated chain of islands. The geographic positioning could make the area harder to reach, making poor service easy to blame on the provider.
Atmos sees opportunity.
The next chapter
The director of the VIWMA wants to rebuild its island-wide, reputable name.
Recently, she greenlit an odor misting system around the Anguilla landfill, which aims to contain foul odors and amend the agency’s relationship with the bordering airport.
If you believe Atmos products and equipment could boost your environmental remediation plan or waste management system, let’s talk today.
What happens when two of the industry’s best join forces? Meet Atmos Technologies.
Atmos brings two of the leading municipal solid waste and environmental remediation daily cover and odor control providers under one roof.
Rusmar, Inc. was the innovator of foam daily cover application systems for landfills and environmental remediation sites across the county. Its combination of cutting-edge chemistry and versatile, heavy-duty application equipment have helped site teams make quicker, cleaner, cheaper work of covering trash or impacted soil.
NCM Odor Control provided a comprehensive stable of portable and permanent misting systems that kept odors, dust and emissions under control at landfills, transfer stations, remediation sites and more across North America. Today, Atmos Technologies reaches wider, digs deeper and does more to keep your neighbors happy, your sites compliant and your bottom line in the black.
Learn more about the new Atmos Technologies.
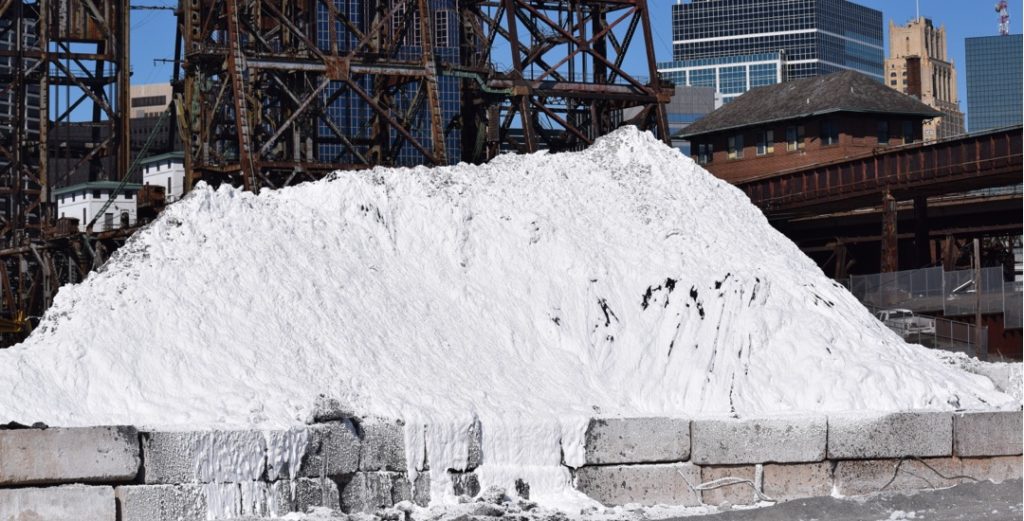
For 61 years, one of New Jersey’s public utilities operated a manufactured gas plant (MGP) on the right bank of the Passaic River, a stone’s throw from central Newark.
Squeezing gas out of coal had been the best way to heat homes and cook meals until natural gas emerged as the superior fuel in the mid-20th century.
MGPs closed in droves in the intervening decades, including this one in 1987. But it left behind a nasty yet familiar legacy of any MGP: coal tar in the topsoil.
Left unchecked, this byproduct of gas manufacturing can leach into groundwater or, when exposed, release foul smells and dangerous vapors. A badly needed remediation finally launched in 2020.
Action plan: open-air in-situ soil stabilization
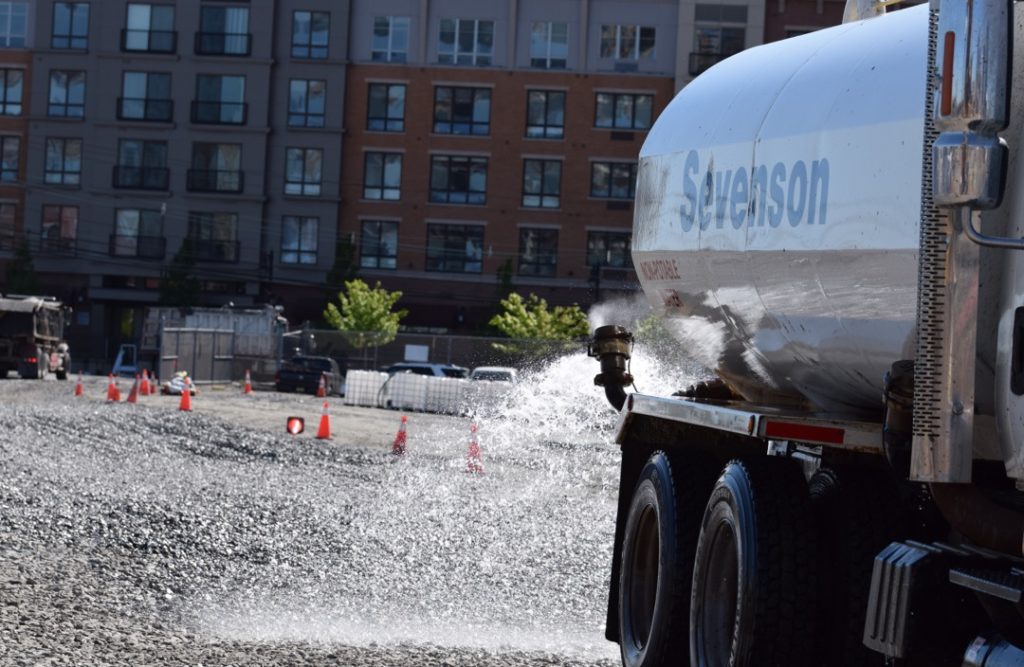
Excavating impacted soil and replacing it with clean fill is the traditional remediation method, but it wouldn’t work here because there was so much of it to move.
Instead, in-situ soil stabilization (ISS) was identified as the ideal remediation. In this process, the impacted earth is left in place and injected with specialty grout that prevents leaching once it cures.
Generally, ISS remediation is less than half as costly as excavating impacted soil and replacing it with clean fill. A more economical model, maybe, but also more complex. Only exceptionally skilled contractors can do it, and they require some exceptional products and equipment to do it right.
But Sevenson Environmental Services’ bona fides speak for themselves.
Founded in 1917, the company has been a major environmental remediation player practically since that category emerged in the 1970s. (Sevenson was among the specialists contracted for the cleanup of the infamous Love Canal dumping ground in Niagara Falls, NY — the country’s first Superfund site.)
They had two options:
- One option was to stabilize the soil under the cover of massive white tents. These tents — and the air filtration systems often accompanying them — are an effective method for containing dust, odors or harmful vapors.
- The other option was to remediate in open air, relying on portable measures to keep odors and VOC emissions under control.
Sevenson chose the latter due to the sheer volume of impacted soil they needed to address. At over 410,000 cubic yards, this is the largest active ISS project in the country. It would be faster, Sevenson reasoned, to do the work continuously instead of stopping and re-starting work every time a tent was dismantled and relocated.
And because they chose ISS over conventional excavation, the project would generate far less truck traffic, reduce fuel use and labor hours, and eliminate the need for added odor and vapor control for impacted soil in transit.
It all hinged on whether Sevenson could keep odors and vapors in check.
Foam coverage is essential to stopping odors and vapors
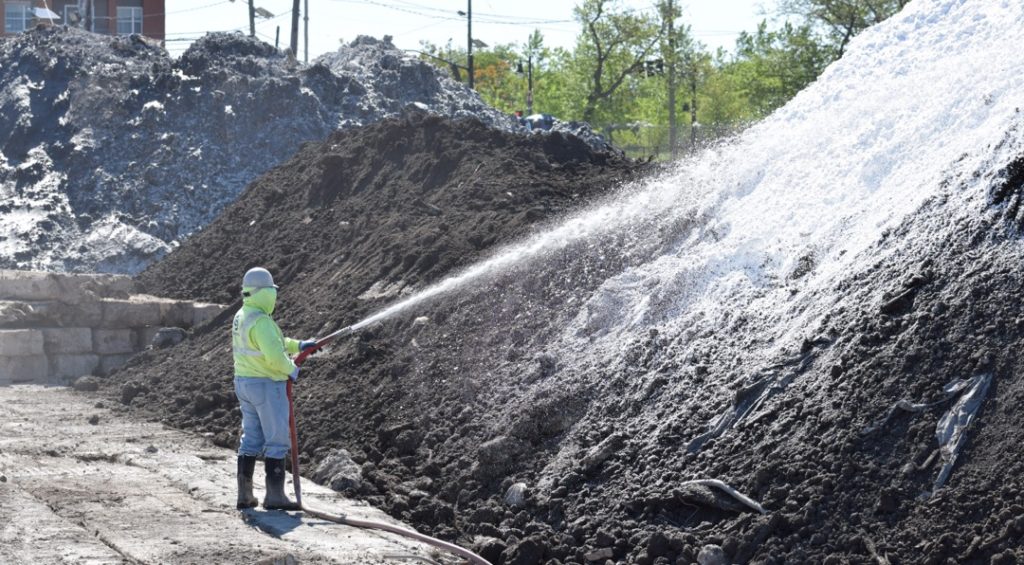
Though the bulk of the impacted soil at this former MGP site will stay where it is, excavation of topsoil to prepare for ISS is still necessary.
Atmos Technologies’ trailer-towed PFU 400/25 foam application system was among Sevenson’s initial fleet of equipment brought to the job site.
To keep odors and vapors from escaping the work site, operators use the system to spray Atmos Shield 645 Foam Concentrate over excavated piles as well as over the earth exposed by the digging. The water-based foam solution provides immediate suppression of odors, dust and VOCs.
Sevenson was familiar with this equipment and product, having utilized it on a handful of prior remediation projects.
An alternative mist odor control product rounds out remediation
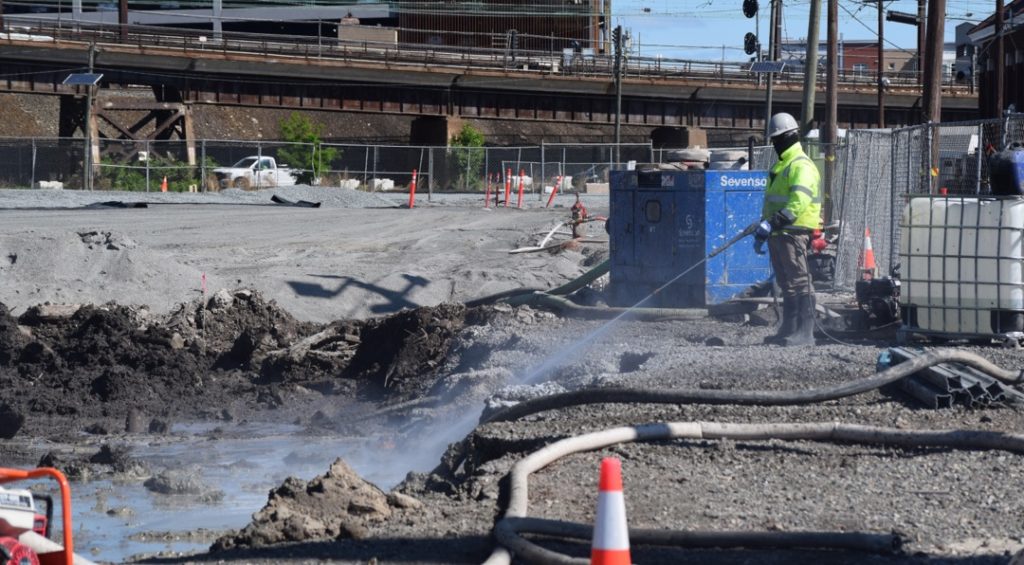
Spraying foam over impacted soil was not the only necessary measure taken at the site. The process of digging into the ground and hauling out dirt results in the release of strong odors and vapors that must be treated right away.
To do this, crews utilized odor-neutralizing mist that’s sprayed directly over the working area during excavation. Sevenson had already lined up a provider of this chemical and system prior to work beginning.
But shortly after excavation began, Atmos representatives asked whether Sevenson was interested in trying one of our mist odor control products instead. We felt our SLSuper Neutralizer Concentrate would work better, and we knew that Sevenson wouldn’t need to use as much volume of product if they switched.
Sevenson agreed to conduct a comparison of the chemicals to see which worked best. Importantly, a third-party consultant and the project’s community liaison each attended the experiment. Given the high volume of odor neutralizer this project would require over time, improved performance at lower doses could represent a significant savings that Sevenson could pass along to the utility.
The experiment confirmed our suspicion. Agreement among Sevenson, the consultant and the liaison was unanimous: Gallon for gallon, the oil-based SLSuper we suggested performed better.
Sevenson estimated that making this switch resulted in a 15% savings on the $3 million they expected to spend on such chemicals. $450,000 is nothing to sneeze at, but additional savings on the horizon might make it look like pocket change.
Reaping the rewards of speed
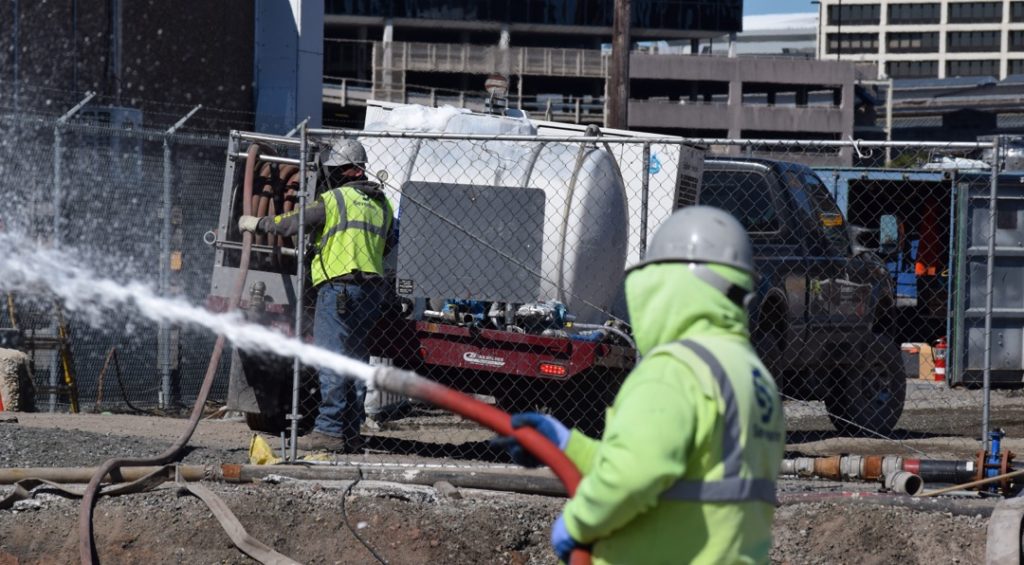
Now sourcing both the mist odor neutralizer and the foam coverage chemicals and equipment from a sole supplier, Sevenson reduced some of the administrative and logistical burdens on their project management team. The cost of all the equipment and all the chemicals is covered under one usage agreement.
But as the project progressed, it became clear that the decision to address odors and vapors with portable equipment in open air would pay off, too.
Due to the toxicity of the soil at the site, the project’s initial contract stipulated that no excavation area could exceed 10,000 square feet. If it was any larger, an unacceptable volume of dangerous vapors could escape the work site if control measures failed.
But Sevenson’s team and the utility each realized that Atmos’s control measures performed so well they could bump that number up. With the utility’s permission, Sevenson’s teams began excavating areas as large as 30,000 square feet at a time without any additional release of dangerous vapors.
And because Atmos delivered temperature-controlled bulk storage tanks to the work site, Sevenson’s operators kept up with the increased pace and volume of foam coverage without any problems.
Sevenson was moving fast, and it had a significant impact:
- The work site features underground natural gas delivery piping that serves surrounding communities. Crews can only excavate after first cutting and capping the piping network.
- That means excavation could only occur from May to October, opposite the “heating season.” Prior to the heating season, Sevenson needed to re-install the gas lines.
- Taking advantage of permission to excavate larger areas, Sevenson finished their excavation-heavy first phase of the project two months early.
- Sevenson estimates daily operating costs at $80,000. Two months translates to a savings of around $3.2 million.
A community reclaims its space
Even now, the Passaic drifts past a work in progress. But that work is a lot farther along than initially planned.
Originally targeted for completion in March 2023, Sevenson wrapped up its remediation phase in late 2021.
That’s saved the utility a lot of money. Even better, it means any plans for the cleaned-up site can kick into motion sooner — no doubt a boon to the region’s economic forecast.
But the most important impact of an early completion?
A year of burden and bother on the thousands living and working nearby was shaved off the project.
For our part, we’re thrilled that our products and equipment have helped make a difference on a project we know will help people take a part of their hometown back.
Interested in learning what new doors the right environmental remediation products and equipment can open for you? Let’s talk.